Customer case: Bylderup-Bov Water Treatment Plant
Despite several expansions and modernisations throughout time, it was time to replace the old water treatment plant in Bylderup-Bov, dating back to 1936. A new, modern and future-proof waterworks with closed filter system, with Kemic Water Technology as turnkey contractor. Read about the process and result in this article.
– We could tell from visiting other water treatment plants that the waterworks from Kemic were simple and looked good, says Jens Martin Thomsen, operations manager at Bylderup-Bov Water Treatment Plant. That was one of the main reasons for selecting Kemic as the supplier.
The new waterworks has been in operation since late 2020 and delivers 100.000 cubic meters of water a year to approximately 540 customers. A few are heavy consumers – more than half of the yearly water supply is delivered to the farms in the area, which requires high level of operational reliability.
Ring connection, frequency control and alternation provides operational reliability
The demands for high levels of operational reliability are the reason the waterworks is ring connected to the other water treatment plant in the village, Bylderup/Lendemark Water Treatment Plant. In addition, the plant now has frequency control for gentle extraction, as well as automatic alternation between the three groundwater boreholes which Bylderup-Bov Water Treatment Plant extracts water from.
– At the old waterworks, we had manual alternation between the boreholes. In one of the boreholes, the lime stone concentration is a tiny bit bigger than the others, so whenever we had complaints about the amount of lime stone in the water, I was sure which borehole we were extracting from at the time. Now the water from the boreholes are mixed automatically, which works really well for consistent water quality. The advice and support from Kemic has been essential in that regard, Jens Martin explains.
Curiosity produces knowledge
Jens Martin Thomsen and the board of Bylderup-Bov Water Treatment Plant are inquisitive by nature, with great interest for the construction of the waterworks, operations and optimisation. Throughout the establishment of the new waterworks, they have shown great interest for the technical aspects, the result and the water treatment. This is the basis for discussions on a high professional level, says Jan Thomsen, who has been Kemic’s project manager for the new Bylderup-Bov Water Treatment Plant:
– Some customers do not ask many questions. They just want us to make sure everything works. Others are very curious and would like to know how it all works, so that they can also solve minor problems on their own if something comes up at some point. In that case, the conversations get a bit nerdy, and it rubs off on the project that they are so enthusiastic about it. At Kemic, we enjoy working with both types of customers as well as those in between. We meet the customers where they are and deliver the service adjusted to the specific needs of the customer.
For Jens Martin in Bylderup-Bov it’s a matter of ensuring the best and most effective solution in case he meets some kind of problem in the daily operations:
– Unless something is completely wrong, I don’t call right away. I investigate as much as possible on my own so that I can provide the relevant information. Perhaps we can save ourselves a service visit and solve it over the phone, or I can learn something from it and solve it on my own another time. But it’s really nice that they always answer the phone, and all the Kemic folks are nice and service minded talking to.
The good collaboration from the construction process continues in the subsequent service and maintenance collaboration, where Kemic continues to be the provider. In order to ensure a smooth transition from project to operations and service, KEmic’s service manager Anja Pedersen has been involved in the final part of the project.
– It is important for us that the customer experiences a smooth transition when the waterworks is finished. Other technicians take over, since assembly and operations/service requires different skill sets, but we need to make good use of the knowledge about the project that we have in house. That is why I myself and the service technicians have been involved in the final adjustments of the waterworks, so that we can provide the best possible service afterwards, says service manager Anja Pedersen, Kemic.
Turnkey contract saves the customer project management
When Jens Martin Thomsen is asked to give other water treatment plant organisations one piece of advice, it’s to consider well if the contract should be offered as turnkey or smaller deliveries from several suppliers:
– To us, selecting Kemic as turnkey contractor was the right solution. The team that Kemic put together for us simply just works. Everything is tied together, and there are no suppliers pointing their fingers at each other. Everything is solved well, tells Jens Martin Thomsen.
Jan Thomsen from Kemic adds:
– It may sound expensive to go for a total contractor, but don’t forget to consider the resources that goes into project management on the customer’s side when the project is divided into smaller contracts. A new water treatment plant is a giant project that requires lots of coordination – it requires time, which the good people at the water treatment plant organisations does not necessarily have, since most of them also have full time jobs to care for. We have done this many, many times before, so we know what can be challenging and how to handle it before it becomes problematic.
Oftentimes, Kemic use local craftsmen when constructing new water treatment plants. This ensures that knowledge and relevant competencies are nearby.
– In Bylderup-Bov, the blacksmith is almost directly across from the water treatment plant. That’s a big advantage for us as well as the customer to use the local blacksmith in that case. It offers flexibility in the construction process, and to the client, the help is literally neat if the blacksmith is required for tasks and maintenance in the future, and he already knows the waterworks, says Jan Thomsen, project manager at Kemic.
New water treatment plant blending in with the surroundings or a new landmark?
The new Bylderup-Bov Water Treatment Plant is kept in classical architectural style in order for it to blend in with the surroundings. In other cases, the desire is for the local water treatment plant to stand out and be a landmark for the city or the area.
– Just as the technical aspects of the waterworks is adjusted to the local conditions, we also design the building to accommodate the customers wishes, says Jan Thomsen – who, apart from being the project manager, also has designed the new Bylderup-Bov Water Treatment Plant. “Of course we advise about the size and layout of the building and ensure the practical application of the building, but the customer is encouraged to share their dreams about the architectural style before we start designing. Would they like it to be classic design, blending in with the environment, or a more modern building which stands out and signals that here lies something new and exciting?”
Jan’s advice for others who are about to establish a new water treatment plant, is to look for inspiration:
– Visit other water treatment plants – not just the neighbours, but get around the country if you have the opportunity. Listen to the experience of others, look at different options. Find out what you like and don’t like, and talk to the supplier based on that.
Inauguration of the water treatment plant
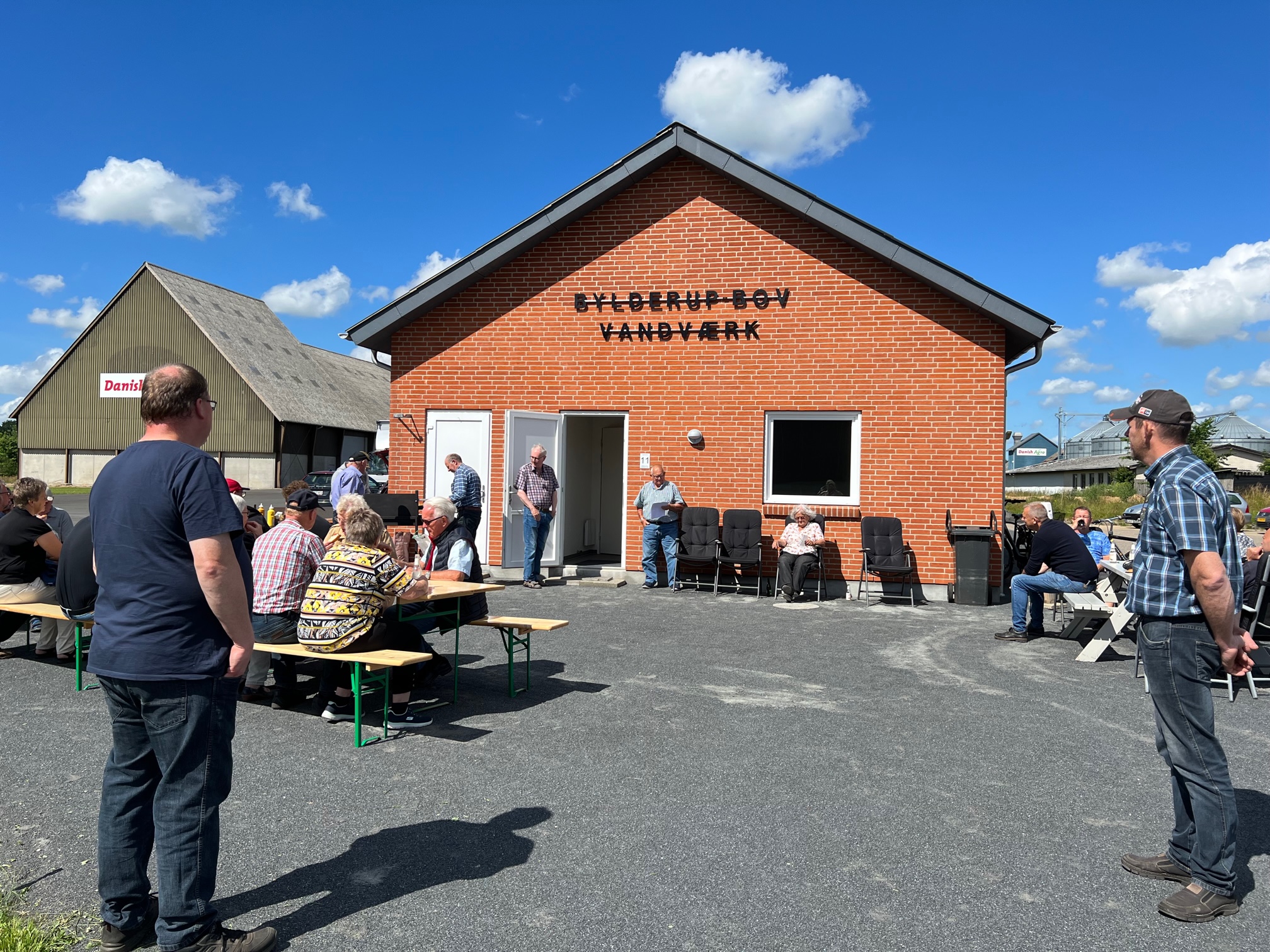
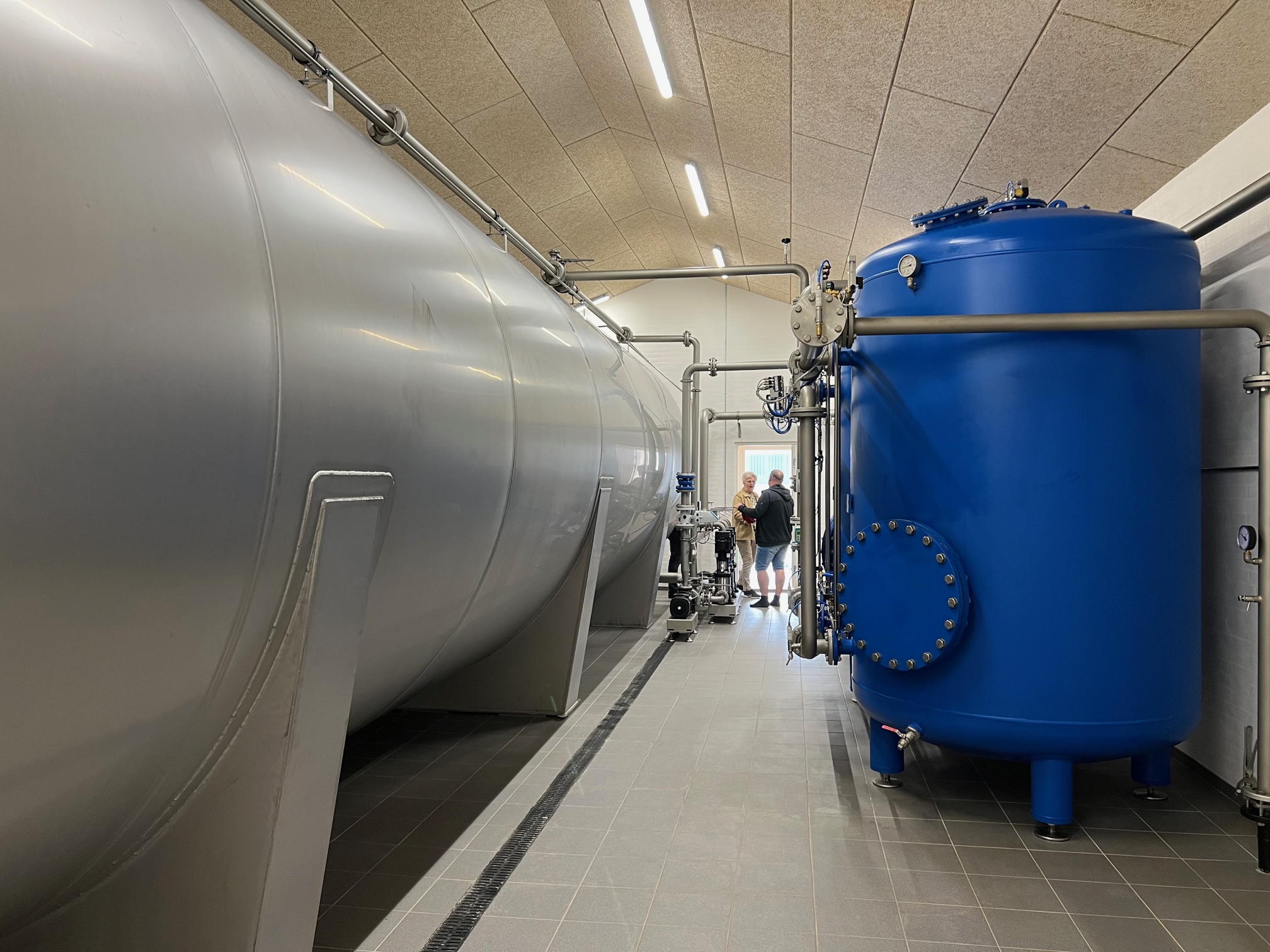
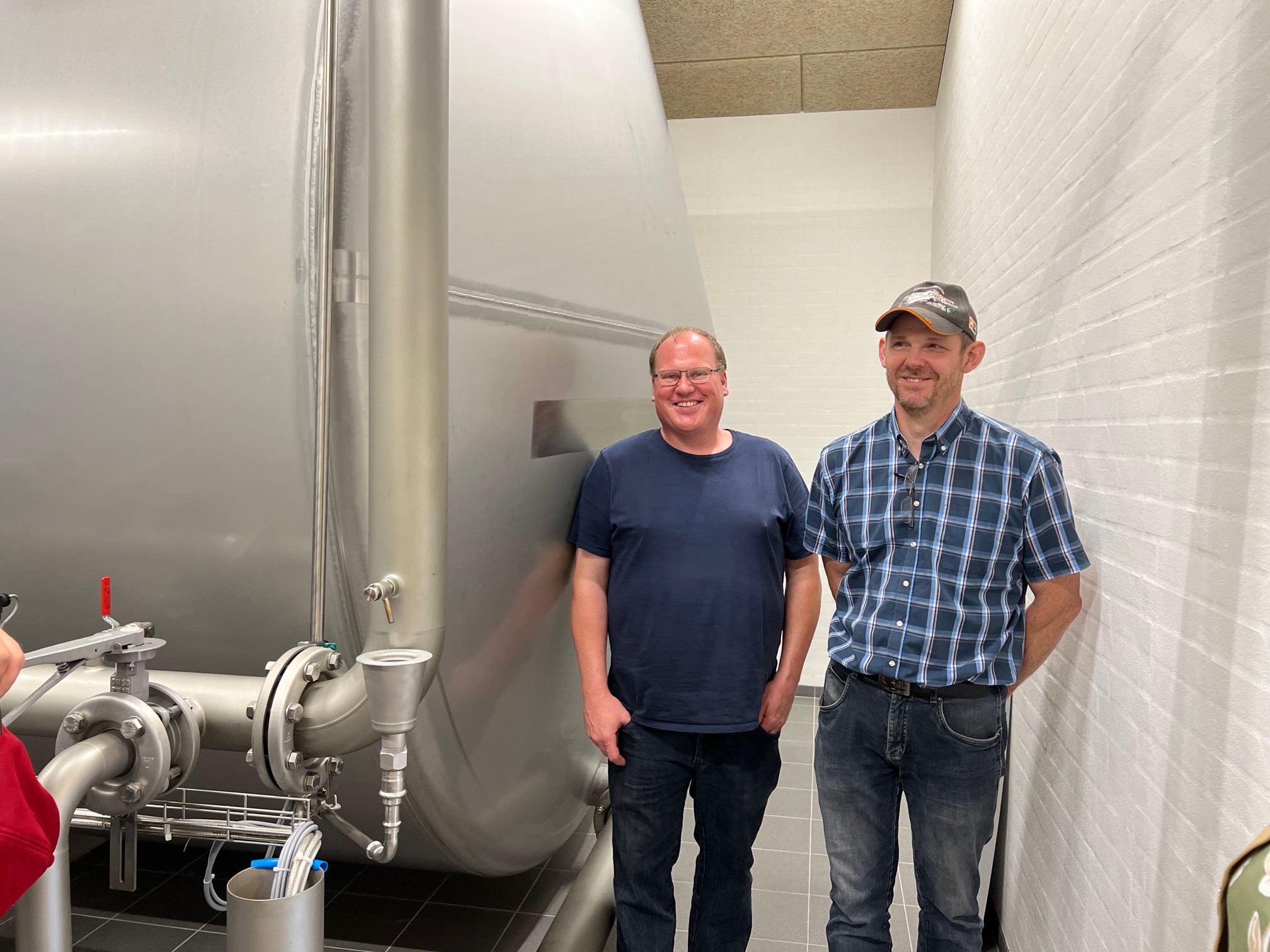
Facts about Bylderup-Bov Water Treatment Plant
- Established in 2020
- One line, one filter set, one clean water tank. With extra connection for possible later expansion of capacity.
- Built with clean water tank bypass for opportunity for inspection.
- Capacity: 100.000 cubic meters a year.
- Water treatment: pressure vessel system, prepared for advanced water treatment.
- Extraction: three boreholes with automatic frequency control and direct fibre connection.
Get in touch
Henrik Nybro Laugesen
E-mail: hnl@kemic.dk
Mobile phone: +45 2655 3280
Phone: +45 7673 3755